Keys to Using CNC Broach Tools
General Speeds/Feeds/Set-up
Speeds – 200 to 550 IPM (Inches per Minute)
Feeds – .0008″ – .0015″ DOC (Depth of Cut per pass)
Examples:
In 4140 – .0008″ DOC at 225 IPM
In Aluminum – .0015″ DOC at 450-550 IPM
In 8620 – .001″ DOC at 250IPM
Speed and Feed Chart
Blog post with downloadable Speed & Feed Chart
MATERIAL | SPEED (Inches per Minute) | FEED (Depth of Cut per pass) |
---|---|---|
Aluminum | 450-550 IPM | .002" |
1215 | 450-550 IPM | .002" |
1018 | 300 IPM | .001" |
4140 (28-32Rc) | 280 IPM | .0008" |
8620 | 250 IPM | .001" |
4140 (55Rc) | 200 IPM | .0006" |
80-55-06 Ductile Iron | 250 IPM | .001" |
17-4 Stainless (30 HRC) | 250 IPM | .001" |
316 Stainless | 250 IPM | .001" |
304/303 Stainless | 225 IPM | .001" |
D2 Tool Steel | 225 IPM | .001" |
6AL-4V Titanium | 225 IPM | .001" |
Ni Al Bronze - C63000 | 225 IPM | .001" |
Inconel/Monel | 200 IPM | .0008" |
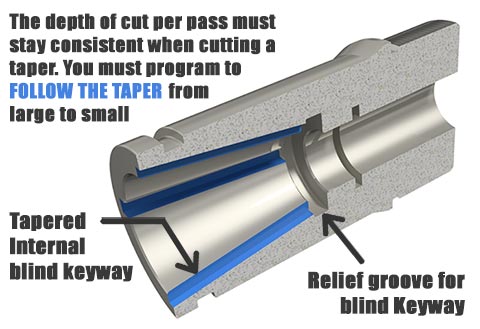
Programming
- Program the tool to drop completely out of the keyway on the retraction, you do not want to drag the nose of the insert back through the slot on the retraction
- Start cut with approx. 1” of space between the face of the insert and the part to allow space to accelerate to full cutting speed
- Failure to have adequate “acceleration space” could result in deflection or tapering
- Broach through the material into open air. This can be accomplished by broaching either though the part or with an appropriate relief cut
- For more info on programming see our Programming page
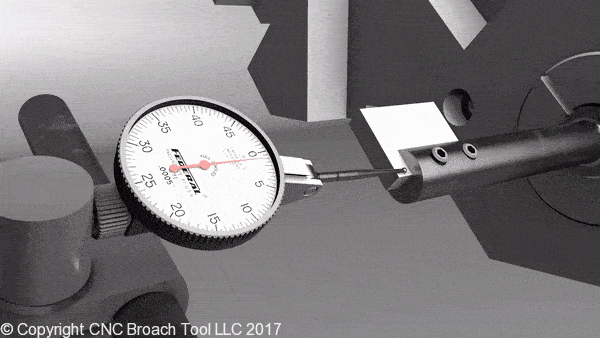
Set-up
How rigidly you hold our tool is the difference between whether it works well or not-
- Use a split sleeve, hydraulic holder, or ER collet which clamps the tool with multiple points of contact from different angles. We do NOT recommend you hold your ER collet shank in a VDI boring bar holder due to overall length created by connecting multiple holders together.
- End mill holders, boring bar sleeves, or solid tool holders with only 2 screws from one direction are not adequate for best insert life
- Take the time to indicate in your “Squareness to the Part at the Tip of the Cut” with gauge blocks
- Our tools are long. If the tool is off in your holder by a .0001”, when you Trig out the length of the tool, 5” out at the tip of the cut you will be hitting the part “off”, dramatically decreasing your insert life
For the Operator
- Do not over-tighten the set screws on our broach tools. Just snug them up.
- Change the insert cutting edge out. A worn out insert will have a rounded, dull edge and won´t cut the part, but rather deflect. The force has to go somewhere.
- Ensure the part you are cutting is clamped rigidly enough to withstand getting hit.
- Use water soluble coolant with a 12-15% concentration for optimum insert life.

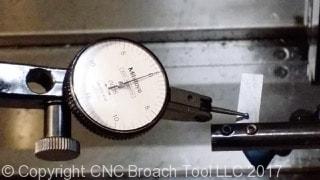
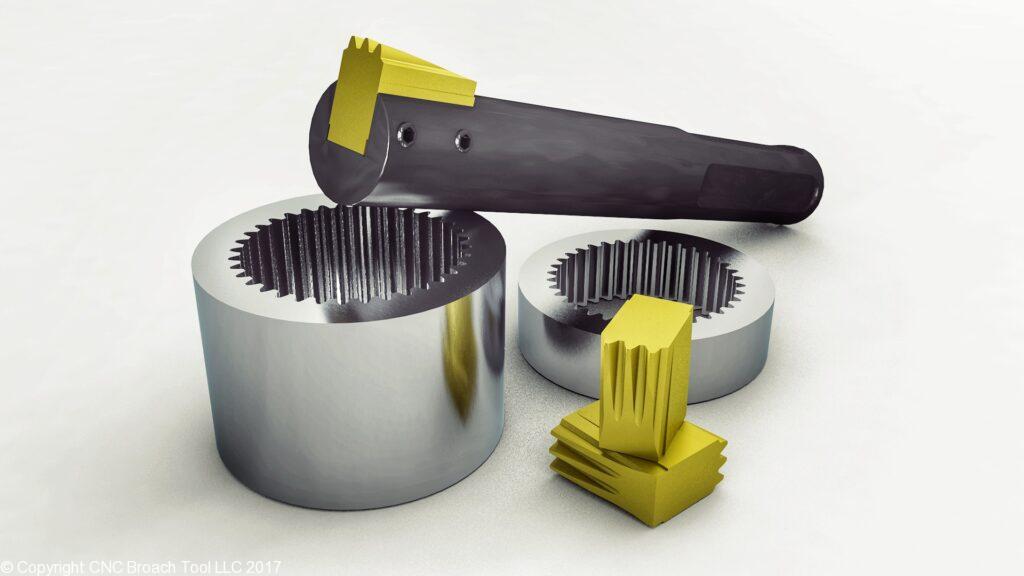
